Blog Post
Understanding Maintenance KPIs: A Guide to Enhancing Your Operations
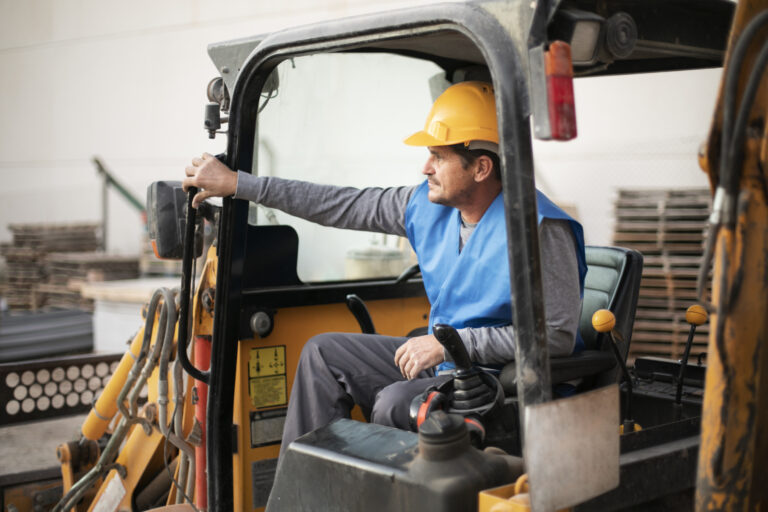
Understanding exactly what a KPIs is and how to tie them to overall business objectives can help. Here are some tips on selecting the best ones for your organization and how to track them more easily so that you can reap the benefits.
Understanding Maintenance KPIs: A Guide to Enhancing Your Operations
Companies have talked about key performance indicators (KPIs) for years. Everyone understands that having a firm grasp on the best KPIs for your organization means reducing downtime and boosting revenue. Yet, in the real world, when critical equipment requires reactive maintenance on a regular basis, it’s hard to prioritize setting up KPIs and strive for world-class standards.
Understanding exactly what a KPIs is and how to tie them to overall business objectives can help. Here are some tips on selecting the best ones for your organization and how to track them more easily so that you can reap the benefits.
What is a Maintenance KPI?
A KPI measures the performance of specific tasks, processes, groups, or team members. Maintenance KPIs that are well-selected to be met within a particular time frame can help organizations boost production, decrease costs, improve safety, and gain efficiency. KPIs work hand-in-hand with metrics: metrics measure the steps toward a goal while the KPI is the goal itself.
Choose Your KPIs
It can be difficult to select the right KPIs for your organization because of the sheer number of possibilities. Many can appear to be great goals to strive for, but if they don’t fit your company’s goals and strategy, they will not be the right choice for your business.
Ideally, you should select five or fewer KPIs for any given period. They need to be very focused on improvements, strategy or long-term growth while supporting your company’s overall goals. It’s important to realize this will be different for every organization. For example, one manufacturer may want to reduce production time by 25 percent, another to decrease safety incidents to under 2 percent, while a third might want to boost customer satisfaction scores to more than 98 percent. Each of these could carry a KPI, but not all will be ideal for every organization. Remember KPIs are not forever; they will change over time and as your company grows and matures.
Finally, don’t forget to obtain buy-in from your managers and leaders. Maintenance supervisors will be closer to the pressing problems at the technician and production level. C-suite executives need to solicit their feedback, understand their struggles and listen to their suggestions before selecting the five KPIs.
Top Ten Maintenance KPIs
While each company will be unique, many share commonalities on their overall goals of reducing repair times, boosting efficiency, and decreasing costs. Check out these top ten for inspiration in selecting your three to five KPIs.
1. Equipment Downtime
You can create a KPI around equipment downtime in one of two ways. You can either try to reduce the amount of time your equipment is unavailable due to emergency breakdowns, or you can work to increase how often a machine is doing what it’s supposed to do.
The world-class unscheduled downtime less than 10 percent while asset availability best practice is greater than 90 percent. Aim for these goals in incremental phases depending on where your company currently sits.
2. Maintenance Backlog
By monitoring how many work orders exist in your system, you can determine appropriate staffing needs. Few or no work orders sitting in the backlog probably means you are overstaffed and could reassign some resources elsewhere. However, a high number of backlogged work orders may signal a need to hire more technicians. Best practices suggest that each technician should have about two weeks of pending work.
3. Mean Time Between Failure and Mean Time to Repair
Mean Time Between Failure (MTBF) tracks the time between each equipment failure for one asset and then finds the average. Once you have a baseline, set intermittent goals for reducing MTBF.
Mean Time to Repair (MTR), on the other hand, looks at the period from the moment of failure to when the asset is back in working order. Account diagnosis, planning, scheduling and the repair itself plays a role in this KPI, and organizations are tasked with finding inefficiencies to reduce MTR.
4. Overall Equipment Effectiveness
Overall Equipment Effectiveness (OEE) tracks the overall performance of a company, looking at asset availability, performance efficiency, and product quality. World-class levels are a minimum OEE of 77 percent.
5. Planned Maintenance Percentage (PMP)
Planned Maintenance Percentage (PMP) measures how much of an organization’s total maintenance is planned. Planned maintenance is always less costly than emergency maintenance. Divide the number of planned maintenance hours by total maintenance hours and see how close you are to best-in-class businesses that report at least an 85 percent PMP.
6. Schedule Compliance
Schedule Compliance monitors the percentage of time that a company actually completes a scheduled work order. Best-in-class standards are 90 percent or greater for this KPI.
7. Maintenance Cost as Percent of Replacement Asset Value
By measuring how cost effective your maintenance program is, you can determine your maintenance cost as a percent of replacement asset value. World-class companies keep this KPI around an impressive one percent.
8. Average Days to Complete Work Orders
Many companies may be focused on how quickly work orders can be completed as a measure of efficiency. However, be sure you don’t end up sacrificing quality for speed. If you select this KPI, you’ll want to balance it with ones that measure failure rates.
9. Percentage of Work Covered by Work Order
It’s important that maintenance work is recorded in a computer system in order to provide data for smart future decisions. This KPI tracks that, and the goal should always be 100 percent. However, you’ll want to set this incrementally and ensure that your next KPI is attainable.
10. Maintenance Overtime
While overtime may not be completely avoidable, you may be able to hold it to a best-in-class level of around 5 percent. Similar to the maintenance backlog KPI, this one can help you make solid labor decisions. Too much overtime may mean you need to hire more technicians while no overtime may indicate overstaffing.
Tracking KPIs
Many technological solutions exist today to help companies track KPIs. Worth the investment, an effective system will help you understand asset costs and reduce unscheduled downtimes. Explore the different options available like Gemini Smart, and be sure to research user friendliness and reporting and analytical capabilities.
Whatever tool you select should allow you to review your selected KPIs frequently, giving you an easy way to update, replace or celebrate these important maintenance measurements.
Stay up-to-date with the best maintenance tips delivered right to your inbox.
Subscribe to our newsletter for regular updates.