Blog Post
The Importance of Identifying Performance Measures
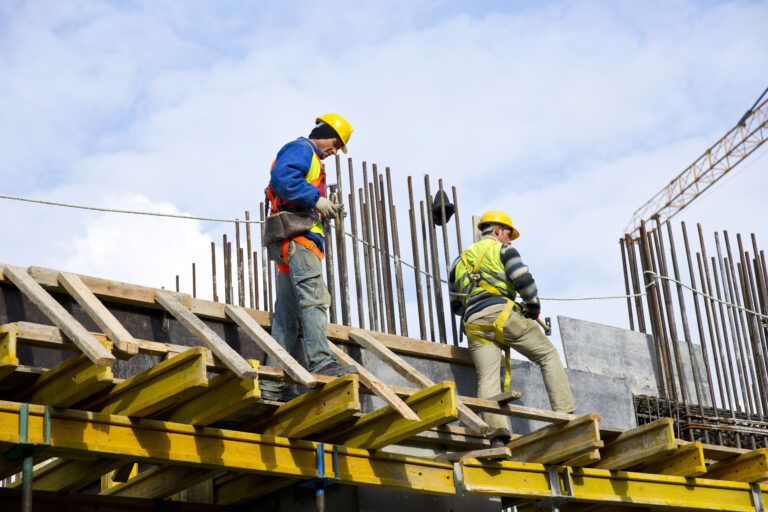
When a critical asset goes down unexpectedly, it’s natural that a maintenance team moves to an all-hands-on-deck mentally, working to restore that piece of equipment. Yet without key performance measures, it can be difficult to know if you’re making any overall improvements in your processes, or just constantly struggling to stay afloat.
The Importance of Identifying Performance Measures
It’s easy to get swept up each day with all those urgent and important matters that come across our desks. When a critical asset goes down unexpectedly, it’s natural that a maintenance team moves to an all-hands-on-deck mentally, working to restore that piece of equipment. Yet without key performance measures, it can be difficult to know if you’re making any overall improvements in your processes, or just constantly struggling to stay afloat.
Each organization must begin by evaluating its current situation and selecting just a few key performance indicators (KPIs) to start moving the needle. It’s important to remember that this will be different for every business; start-ups or small companies will have challenges that differ from established manufacturers with larger teams and more resources.
Common Performance Measures
When setting up maintenance KPIs, you may want to focus initially on minimizing repair times, boosting efficiency, and cutting costs. Below are eleven essential KPIs to consider for your company. It’s advisable to start with a maximum of three to five to ensure focus and manageability.
- Equipment Downtime. Evaluate equipment downtime by analyzing two main aspects: the frequency of emergency breakdowns and the availability of equipment for its intended tasks. Top-performing standards suggest unscheduled downtime should be below 10 percent, while equipment availability should exceed 90 percent. Use these benchmarks to guide your downtime KPI.
Remember to set measurable, incremental goals within specific time frames. Instead of reaching immediately for world-class standards, begin with a goal for a 10 percent improvement for your most critical asset over the next six months instead.
- Maintenance Backlog. Assess the number of pending work orders in your system to gauge whether your staffing levels are appropriate. A minimal backlog might indicate overstaffing, while a large backlog could signal a shortage of maintenance personnel. Ideally, world-class metrics suggest a backlog equivalent to about two weeks’ worth of work per technician. Determine a KPI that aligns with this standard.
You can also use this data to better balance work among technicians and also to determine which technicians are performing well and which ones may need additional training.
- Mean Time Between Failures (MTBF). This KPI measures the average time between equipment failures for specific assets. By evaluating MTBF, you can set realistic goals for improving the reliability of critical equipment based on historical performance.
Remember that it’s important to have accurate, high quality data to evaluate this and other KPIs accurately. Be sure to establish well-understood processes and ongoing training so that technicians know what information and how to enter it properly on their work orders.
Once data is collected, you may want to look at adding continuous monitoring processes by using sensors, implementing a preventive maintenance program, or consider scheduled testing to help reduce the MTBF.
- (MTR). Closely related to MTBF, MTR tracks the time required to diagnose, plan, schedule, and complete repairs from the moment a failure occurs. This KPI helps identify process inefficiencies. Reducing MTR can yield immediate improvements once inefficiencies are addressed.
Begin by auditing your current processes and identify bottlenecks. You may want to better leverage the knowledge base of your teams, discover ways to speed up the initial response time, make support documents and manuals easier to access, and streamline the process to record completed work through mobile apps and the use of images.
- Overall Equipment Effectiveness (OEE). OEE measures the overall performance of a facility by evaluating equipment availability, efficiency, and product quality. World-class OEE benchmarks are typically 77 percent or higher. Determine your current OEE and consider ways to reach or surpass this standard.
Six ways to reduce OEE include avoiding equipment failure, expedite setup and adjustments, minimize idling and minor stops, troubleshoot reduced speed, minimize process defects, and prevent reduced yield.
- Planned Maintenance Percentage (PMP) This KPI indicates how much of your maintenance work is planned versus reactive. Planned maintenance tends to be more cost-effective and less disruptive. Calculate PMP by dividing planned maintenance hours by total maintenance hours over a specific period. Aim for a PMP of 85% or higher to align with world-class practices.
Companies who select this KPI will be able to reduce unplanned downtime, drop maintenance costs, decrease emergency situations, and give more control over maintenance costs.
- . Track the percentage of scheduled work orders completed on time. High schedule compliance is crucial for maintaining an effective maintenance process. World-class standards suggest aiming for a compliance rate of 90 percent or above.
Begin by analyzing results and trends, and be sure to ask your team to participate in this analysis. This will help you better understand your organization and make smarter decisions.
- Maintenance Cost as a Percentage of Replacement Asset Value (RAV). This KPI assesses the cost-efficiency of your maintenance program by comparing maintenance costs to the replacement value of assets. World-class organizations often maintain this ratio around 1%.
Identify a performance indicator that reflects maintenance cost relative to RAV for your company. Then, set up a timeframe and work toward it.
- Average Days to Complete Work Orders. This metric measures how quickly work orders are completed. While speed is important, balance this KPI with failure-related metrics to ensure that work is not rushed at the expense of quality.
Gemini Smart offers a wide range of tools to help organizations better evaluate this metric.
- Percentage of Work Covered by Work Orders. Evaluate how much of your maintenance work is documented in your system. Accurate data collection is crucial for informed decision-making.
While aiming for 100% coverage is ideal, set a realistic target based on your current capabilities. If you’re struggling in this area, you may want to shoot for a 10 percent improvement over the next year before begin working toward perfection.
- Maintenance Overtime. Track overtime to determine appropriate labor levels. Some overtime is acceptable, especially for exceptional circumstances. However, consistently high overtime can lead to technician burnout and increased costs. Aim for a maintenance overtime rate around 5 percent to align with world-class standards and monitor trends to address any negative patterns.
By carefully selecting and monitoring these KPIs, you can enhance your maintenance practices and drive improvements in efficiency, effectiveness, and cost management.
Stay up-to-date with the best maintenance tips delivered right to your inbox.
Subscribe to our newsletter for regular updates.