Blog Post
Scheduled Maintenance (or Predictive Preventive Maintenance)
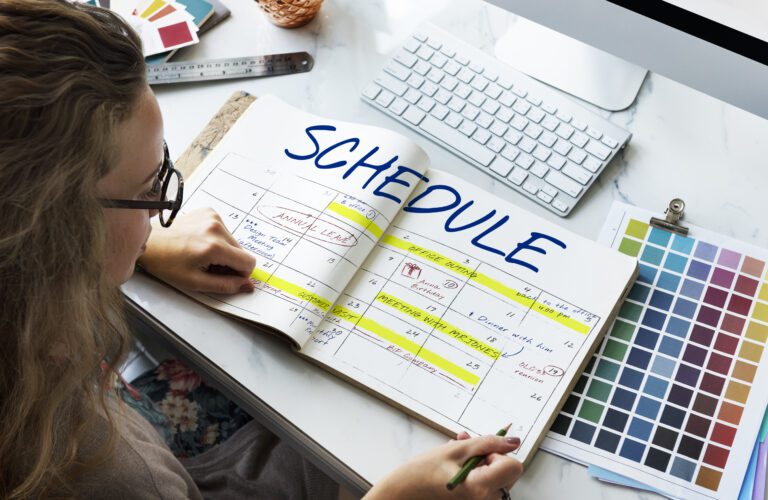
Scheduled Maintenance (or Predictive Preventive Maintenance).
Scheduled maintenance or predictive preventive maintenance is an advanced approach to managing equipment and systems.
Maintenance activities are planned based on the actual conditions of machinery, monitored through real-time data or regular inspections.
This type of maintenance relies on analyzing specific parameters to predict potential failures and intervene before they occur.
Key Features
Based on real data:
Utilizes sensors, analytical tools, and software to monitor the condition of machinery.
Analyzed parameters include temperature, vibration, pressure, noise, corrosion, lubrication, etc.
For example, vibration sensors can detect imbalances in a motor or a defective bearing before it breaks.
Failure prediction:
Data analysis identifies abnormal trends or signs of wear and tear.
If the system detects a sudden increase in vibrations in a turbine, it can indicate an imminent problem, such as a damaged blade or balancing issue.
Targeted interventions:
Maintenance activities are carried out only when necessary, avoiding unnecessary interventions.
This approach optimizes resources, reduces costs, and extends equipment lifespan.
Practical Examples
1.Construction Sector
1.1 Monitoring cranes and heavy equipment:
Vibration and pressure sensors installed on cranes can detect wear in cables or hydraulic systems.
Action: Schedule maintenance to replace worn parts before a breakdown, ensuring site safety.
Benefit: Prevents machine downtime during critical project phases.
1.2 Monitoring building facades:
Sensors detect structural shifts or water infiltration in complex buildings.
Action: Prompt repairs to address the issue before it escalates.
Benefit: Reduces repair costs and extends the structure’s lifespan.
2.Condominium Management
2.1 Elevators:
Diagnostic systems monitor energy consumption, vibrations, and door operations.
Action: Replace worn components before a failure occurs.
Benefit: Ensures reliability and safety for residents.
2.2 Plumbing and central heating systems:
Sensors detect water leaks or pressure drops.
Action: Immediate repairs to prevent structural damage.
Benefit: Avoids high water bills and waste.
3.Healthcare Sector
3.1 Medical equipment:
Continuous monitoring of critical devices such as ventilators, MRIs, and CT scanners.
Example: A CT scanner shows declining performance due to overheating in its main magnets.
Action: Schedule maintenance to replace the component.
Benefit: Prevents failures that could compromise operations and patient safety.
3.2 Hospital HVAC systems:
Air conditioning systems in hospitals are crucial for maintaining hygiene and infection control. Pressure and temperature sensors detect anomalies.
Action: Clean or replace filters before a malfunction occurs.
Benefit: Ensures optimal conditions and a sterile environment.
4.Public Administration
4.1 Street lighting:
Smart management systems detect malfunctions or abnormal energy consumption in streetlights.
Example: A lamp post reports excessive energy use, indicating a defective circuit.
Action: Repair the circuit before the fault affects other units.
Benefit: Reduces energy costs and ensures continuous service.
4.2 Infrastructure monitoring:
Sensors installed on bridges and roads monitor vibrations and structural shifts.
Example: A bridge shows increased vibrations due to microcracks.
Action: Promptly consolidate the structure.
Benefit: Prevents closures or more costly emergency interventions.
5.Banking Sector
5.1 ATMs and security systems:
Diagnostic tools monitor ATMs and security systems (e.g., safes and cameras).
Example: An ATM shows reduced performance due to a failing hard drive.
Action: Replace the drive before a total failure occurs.
Benefit: Ensures operational continuity and minimizes customer service disruptions.
5.2 HVAC systems in data centers:
Bank servers require constant cooling. Sensors detect temperature increases or inefficiencies in cooling systems.
Action: Immediate repairs or replacement of cooling units.
Benefit: Protects data and ensures banking services remain uninterrupted.
6.Transportation Sector
6.1 Trains and metros:
Predictive diagnostics detect wear in brakes, wheels, and motors.
Example: A train wheel shows imbalances that could lead to derailment.
Action: Replace the wheel during scheduled maintenance.
Benefit: Ensures passenger safety and reduces delays.
6.2 Airports:
Conveyors and escalators at airports are monitored using vibration and temperature sensors.
Example: An escalator motor reports increased temperature due to a defective bearing.
Action: Repair the motor before a complete breakdown.
Benefit: Maintains passenger flow and avoids operational interruptions.
Benefits of Scheduled Maintenance in Specific Sectors
Cost reduction: Prevents expensive emergency repairs and operational downtime.
Safety: Reduces the risk of accidents caused by unexpected failures.
Operational efficiency: Improves service continuity and user satisfaction.
Asset preservation: Helps maintain the value and functionality of infrastructure and equipment.
Scheduled maintenance is a strategic solution for various sectors, making processes more efficient, safer, and sustainable, with tangible benefits for operators and users alike.
Stay up-to-date with the best maintenance tips delivered right to your inbox.
Subscribe to our newsletter for regular updates.