Blog Post
Benefits and Challenges of Preventive Maintenance
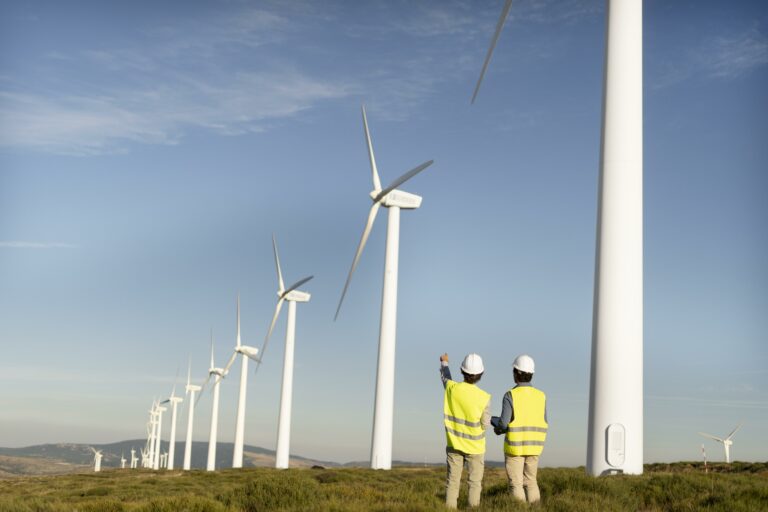
Preventive maintenance is a proactive approach to equipment and asset management that aims to prevent breakdowns and extend asset life by performing regular maintenance tasks. While it offers numerous advantages, it also comes with some challenges that organizations must address.
Benefits and Challenges of Preventive Maintenance
Preventive maintenance is a proactive approach to equipment and asset management that aims to prevent breakdowns and extend asset life by performing regular maintenance tasks. While it offers numerous advantages, it also comes with some challenges that organizations must address.
Understanding both the benefits and challenges will help you optimize your preventive maintenance program, ensuring that it generates the highest return on investment for your organization.
Benefits of Preventive Maintenance
Historically, maintenance has been associated with repairing equipment or machines that are broken. This type of reactive maintenance focus is often not only expensive for manufacturers but also stressful for maintenance technicians. The majority of the benefits revolve around reduced long-term costs, increased efficiency, and improved equipment performance.
- Reduced Downtime. One of the most significant advantages of preventive maintenance is the reduction in unplanned downtime. According to Reliable Plant, focusing on 87 key items reduces unplanned downtime by more than 50 percent over 18 months. By addressing potential issues before they escalate into equipment failures, organizations can ensure continuous operations, avoid costly production halts, and meet deadlines without disruption.
- Extended Asset Lifespan. Regular maintenance tasks, such as lubrication, cleaning, and part replacements, help prolong the life of equipment. Preventive maintenance ensures that assets run more efficiently and experience less wear and tear, delaying the need for major repairs or replacements. This leads to lower capital expenditures in the long term.
- Improved Safety. Well-maintained equipment is less likely to malfunction, reducing the risk of accidents and injuries. Preventive maintenance often includes safety checks, which help identify and address potential hazards before they pose a threat to workers. This promotes a safer working environment and minimizes liability risks.
- Cost Savings. While preventive maintenance requires an upfront investment in time and resources, it leads to significant cost savings over time. Regularly servicing equipment prevents costly emergency repairs, extends asset life, and optimizes energy consumption. The overall reduction in unplanned maintenance and downtime directly translates into financial savings.
- Increased Efficiency. Properly maintained equipment operates more efficiently. Preventive maintenance keeps machinery running at optimal performance levels, which can result in faster production times, lower energy consumption, and higher-quality outputs. It also reduces the likelihood of small problems escalating into larger, more complex issues.
- Enhanced Reliability and Predictability. A well-structured preventive maintenance program helps organizations predict and plan maintenance activities, giving them more control over their operations. This predictability improves resource allocation, as maintenance technicians and spare parts can be scheduled in advance, minimizing disruptions to production.
Challenges of Preventive Maintenance
Although every program has some disadvantages, the challenges with preventive maintenance are often temporary. Most revolve around the time, resources, and effort required to build and implement an effective preventive maintenance program.
- Initial Costs and Investment. Setting up a preventive maintenance program requires an initial investment in terms of time, resources, and technology. Developing maintenance schedules, purchasing necessary tools and parts, and implementing a work order system or computerized maintenance management system (CMMS) can be costly, especially for smaller organizations.
- Resource Allocation. Preventive maintenance requires a dedicated workforce and a commitment of time, which can be a challenge for organizations with limited staff. Additionally, scheduling maintenance tasks during operational hours can result in short-term disruptions, particularly in industries that operate 24/7.
- Over-Maintenance. Preventive maintenance programs can sometimes lead to unnecessary maintenance tasks being performed on equipment that may not require them. Over-maintenance can result in wasted resources, higher costs, and even premature wear of parts. It’s important to strike a balance between proactive maintenance and avoiding excessive intervention.
- Implementation Complexity. Implementing a preventive program can be complex, especially for organizations with a large number of assets or multiple types of equipment. Coordinating maintenance tasks, gathering accurate data, and tracking progress across various departments can be challenging without proper organization and communication.
- Adapting to Equipment Variability. Not all equipment requires the same level of maintenance, and some assets may not fit neatly into standard preventive maintenance schedules. It can be challenging to account for equipment variability, especially if different assets age at different rates or operate under varying conditions. Tailoring maintenance schedules for different types of equipment adds complexity to the process.
- Lack of Immediate ROI. While preventive maintenance saves money in the long term, it may not offer an immediate return on investment (ROI). Organizations may struggle with the perception that they are spending resources on maintenance without seeing immediate tangible results. This can make it harder to justify the costs of implementing a preventive maintenance program, especially to upper management.
Balancing the Benefits and Challenges
To maximize the benefits and mitigate the challenges of preventive maintenance, organizations should focus preventive maintenance efforts on critical equipment and factors that directly impact operations or safety.
Begin by leveraging historical data and condition monitoring to fine-tune maintenance schedules. This can help avoid over-maintenance while ensuring that important tasks are performed on time. A CMMS solution can streamline preventive maintenance activities, reduce human error, and provide valuable insights to help refine the program.
Finally, equip maintenance teams with the necessary skills and knowledge to carry out preventive tasks effectively. Well-trained technicians are key to ensuring that maintenance procedures are followed correctly and that equipment is properly serviced.
Preventive maintenance offers a proactive approach to asset management that can significantly reduce downtime, extend equipment life, and improve operational efficiency. However, it comes with challenges, such as initial costs, resource allocation, and the risk of over-maintenance. By carefully planning and balancing these factors, organizations can successfully implement a preventive maintenance program that delivers long-term value and reliability.
Stay up-to-date with the best maintenance tips delivered right to your inbox.
Subscribe to our newsletter for regular updates.