Blog Post
Differences Between Breakdown Maintenance, Periodic Maintenance, and Scheduled Maintenance Maintenance
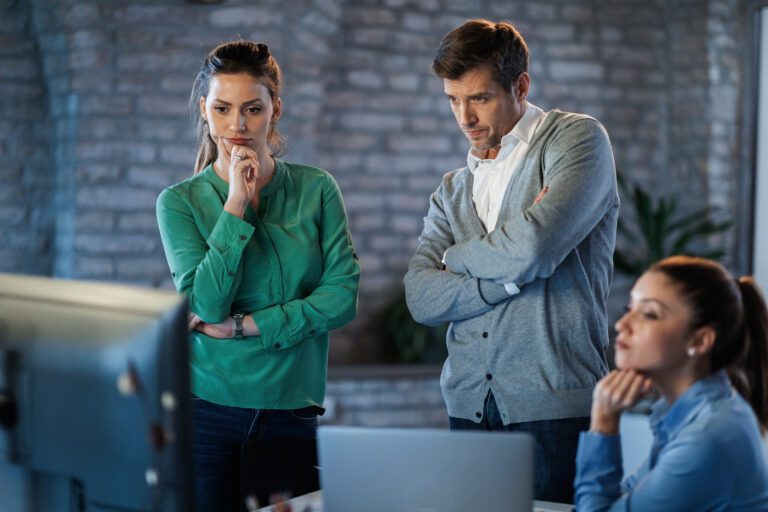
The differences Between Breakdown Maintenance, Periodic Maintenance, and Scheduled Maintenance Maintenance, is crucial for the optimal and safe operation of machinery, systems, or equipment.
Here are the key differences between Breakdown Maintenance, Periodic Maintenance, and Scheduled Maintenance:
1. Breakdown Maintenance (or Corrective Maintenance):
Definition: Maintenance performed when a failure or malfunction occurs.
Characteristics:
Reactive: No preventive actions are taken.
Actions are only initiated after a breakdown.
Primary goal: Restore the system or equipment to working condition.
Typically used in contexts where downtime costs are not critical or failures are hard to predict.
Pros:
No upfront costs for inspections or scheduled interventions.
Suitable for non-critical or low-risk systems.
Cons:
Risk of prolonged downtime.
Higher overall costs if secondary damage occurs.
Potential safety hazards.
2. Periodic Maintenance (or Standard Preventive Maintenance):
Definition: Regularly scheduled maintenance performed at predefined intervals or after a certain amount of usage.
Characteristics:
Based on a fixed time schedule (e.g., monthly, quarterly, annually).
Includes standard activities like cleaning, lubrication, and replacement of worn parts.
Does not consider the actual condition of the equipment.
Pros:
Reduces the likelihood of unexpected failures.
Allows for planned interventions.
Cons:
Maintenance may be performed even when unnecessary.
Additional costs for non-essential inspections or servicing.
3. Scheduled Maintenance (or Predictive Preventive Maintenance):
Definition: Maintenance planned based on monitoring and analyzing the actual conditions of machinery or systems.
Characteristics:
Relies on data and monitoring tools (sensors, vibration analysis, thermography, etc.).
Aims to intervene before visible signs of failure occur.
Includes targeted inspections and interventions based on actual wear and tear.
Pros:
Maximizes the useful life of components.
Reduces unplanned downtime and failure-related costs.
Enhances operational safety.
Cons:
Requires advanced monitoring tools and technical expertise.
Higher initial investment.
The choice of maintenance type depends on the criticality of the system, the cost of downtime, and the importance of safety in the operational context.
Stay up-to-date with the best maintenance tips delivered right to your inbox.
Subscribe to our newsletter for regular updates.